Damen and Huisman have teamed up to eliminate the challenges of today’s cable lay operations. The result of this collaboration is the world’s first motion compensated cable laying vessel (CLV), a fully integrated solution specifically tuned to optimising operability and improving control and accuracy of cable placement.
Cable lay operations are very sensitive to the weather conditions. As a result, operations are typically limited to a significant wave height of 1.5-2 metres, resulting in a workability of approximately 65%. This novel CLV solution can stretch the limits of cable laying and operate in sea states with significant wave heights of up to 3.5m.
Motion Compensated Cable Laying
The Huisman Motion Compensated Cable Lay System compensates the vertical motion of the overboarding chutes, greatly improving the workability of the vessel and expanding its workable season.
This is combined with Damen’s Offshore Carrier (DOC), a proven design featuring high levels of comfort, outstanding seakeeping characteristics and a large deck.
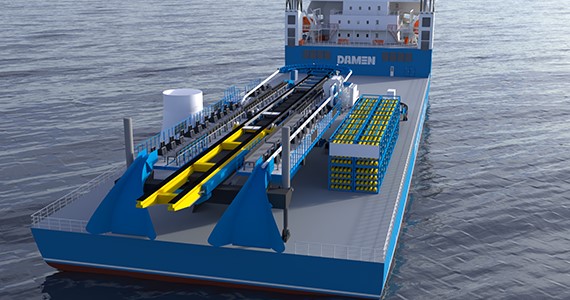

Operational benefits
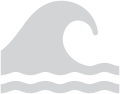
to Hs 3.5m


results in a compact and
efficient vessel
Explore the vessel
CLICK THE MARKERS TO VIEW THE VESSEL FEATURES
- external
- internal
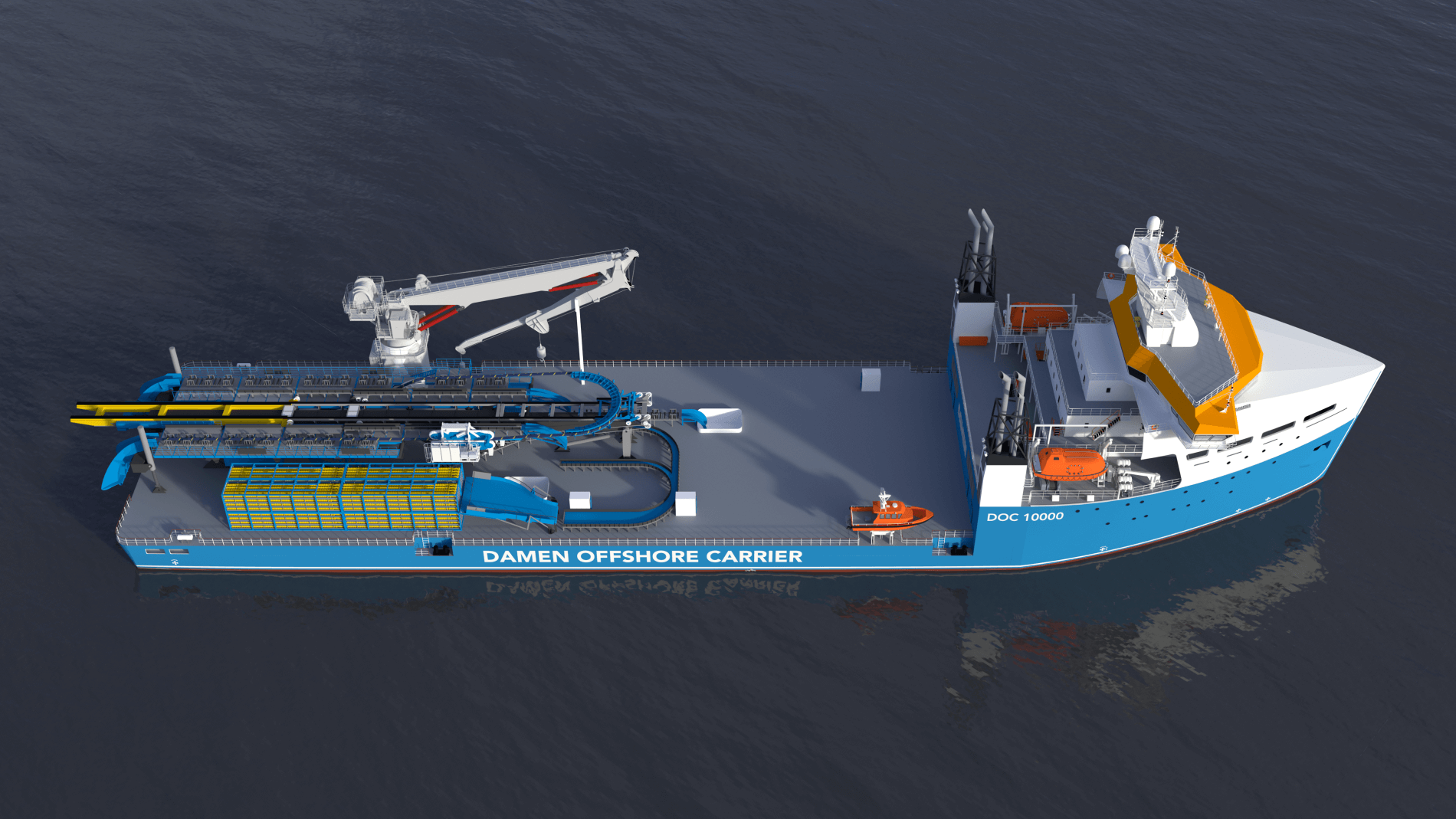
The quadrant is fully restrained from the start of the operation until deployment below the splash zone:
- Increased weather window
- Controlled and time efficient operation
- Increased safety
The quadrant handling system is equipped with a cursor system. The quadrant motions are fully restrained until deployed beneath the splash zone:
- The cursor system prevents damage to the quadrant
- Reduced catenary dynamics
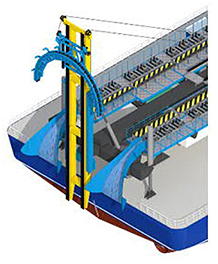
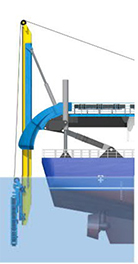
The Motion Compensated Cable Lay System provides significantly improved workability in combination with reduced risk of cable damage in several ways:
- Avoiding overbending of the cable caused by catenary dynamics
- Compression in the cable will not occur due to reduced tension variations
- Touch down point excursions are reduced therefore omitting the damage of the cable, in particular when cornering
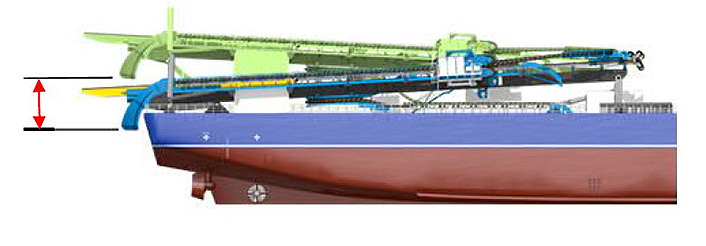
CPS strings are loaded on board in containers and transferred to the firing line using a gutter system
- Containers allow for easy transport and loading
- Height adjustable ramp to extract a CPS from different elevations
- CPS gutter system independent from cable routing allowing parallel operations
- Safe access for personnel to containers
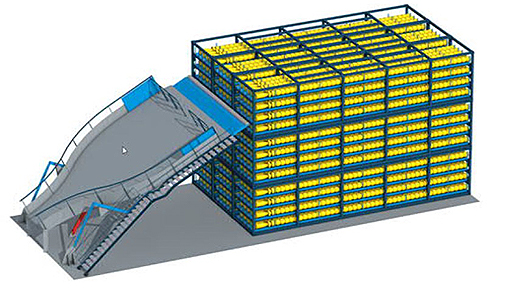
Synchronisation of the pull-in-winch with the central control system ensures better control of pull-in operations
- Improved tension control avoids overbending or compression in the cable
- Controlled from vessel using a secure data connection
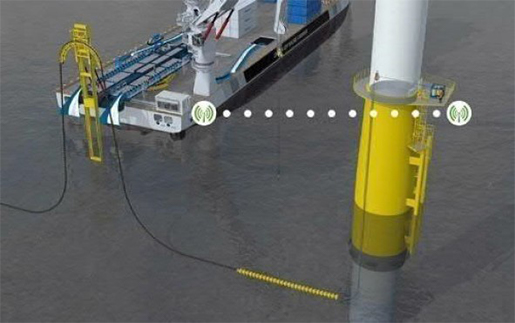
The radius of the quadrant can be adjusted from the maximum bending radius to straight during lowering
- Cable can be abandoned without uncontrolled drop onto the seabed. Cable tension is controlled throughout the operation
- Quadrant can be retrieved when cable is straight on the seabed avoiding torque variations that can cause cable failure
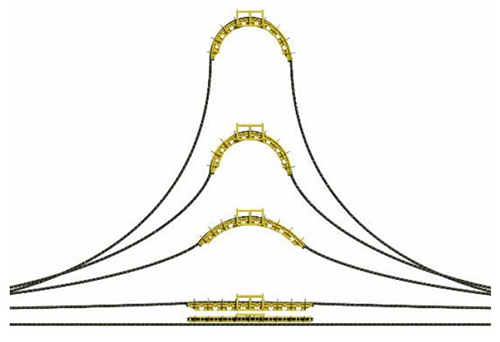
Approximately 600 ㎡ of free deck space is available for placement of additional cargo, container storage or mission specific equipment, in equivalent of 500 t
- Equipment, controls, instruments and furniture are thoughtfully arranged providing optimum functionality and comfortable layout
- In collaboration with our suppliers, a selection of equipment and digitalisation technologies has been made with the aim of making the bridge operation easier and safer without compromising improved performance of the vessel
- An ergonomically designed bridge layout with optimal bridge visibility in accordance with the rules and regulations, 360 degree clear view on the work deck as well as the relevant deck equipment
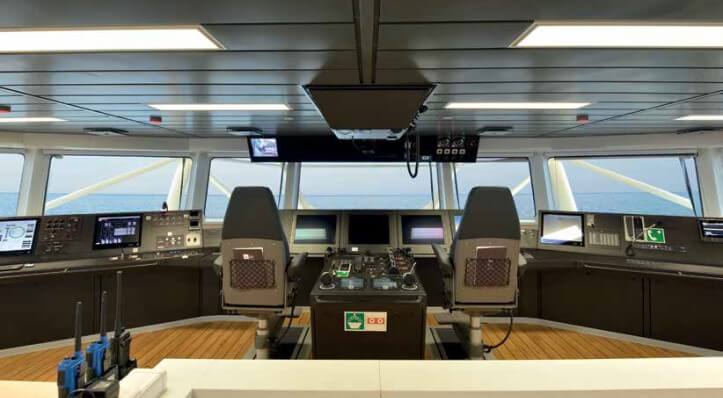
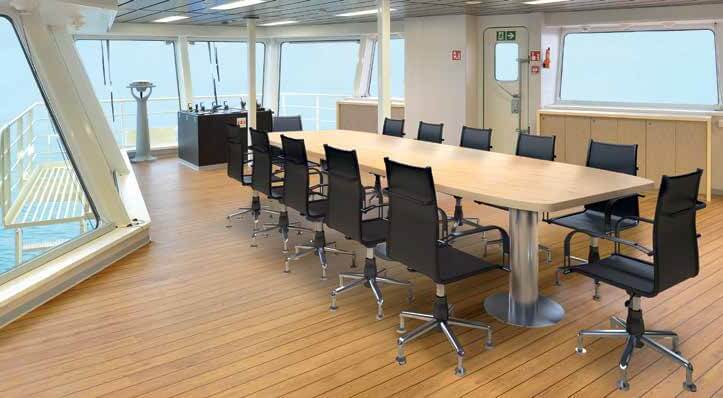
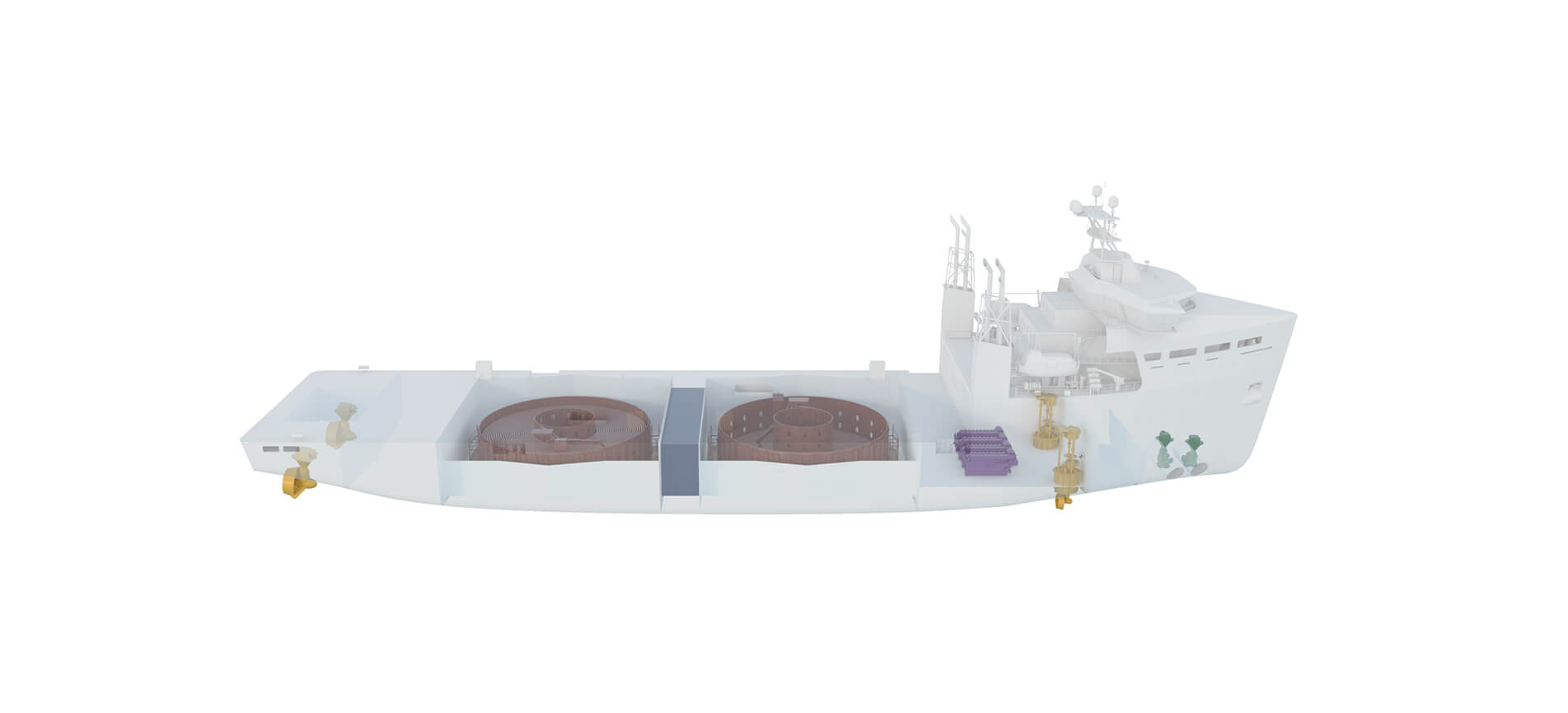
- Ample carrousel capacity (2x 4000 t) to execute any cable lay operation efficiently
- Maximum weather protection of crew and product during loading and operations
- More free deck space for storage, additional mission equipment etc.
- Free surface anti-roll tank is integrated in the vessel
- Positioning at center of the vessel results in optimal roll damping effect
- The anti-roll tank is far from the accommodation, so noise disturbance for crew is minimal
- Vessel enables station-keeping up to Hs 4.2 m (without laying cable)
- Vessel enables harsh weather cable lay operations (up to Hs 3.5m)
- Propulsion set-up:
- Azimuth thrusters 2x 3100 KW
- Retractable thrusters 2x 1400 KW
- Tunnel thrusters 2x 1400 KW
Explore the vessel
- external
- internal
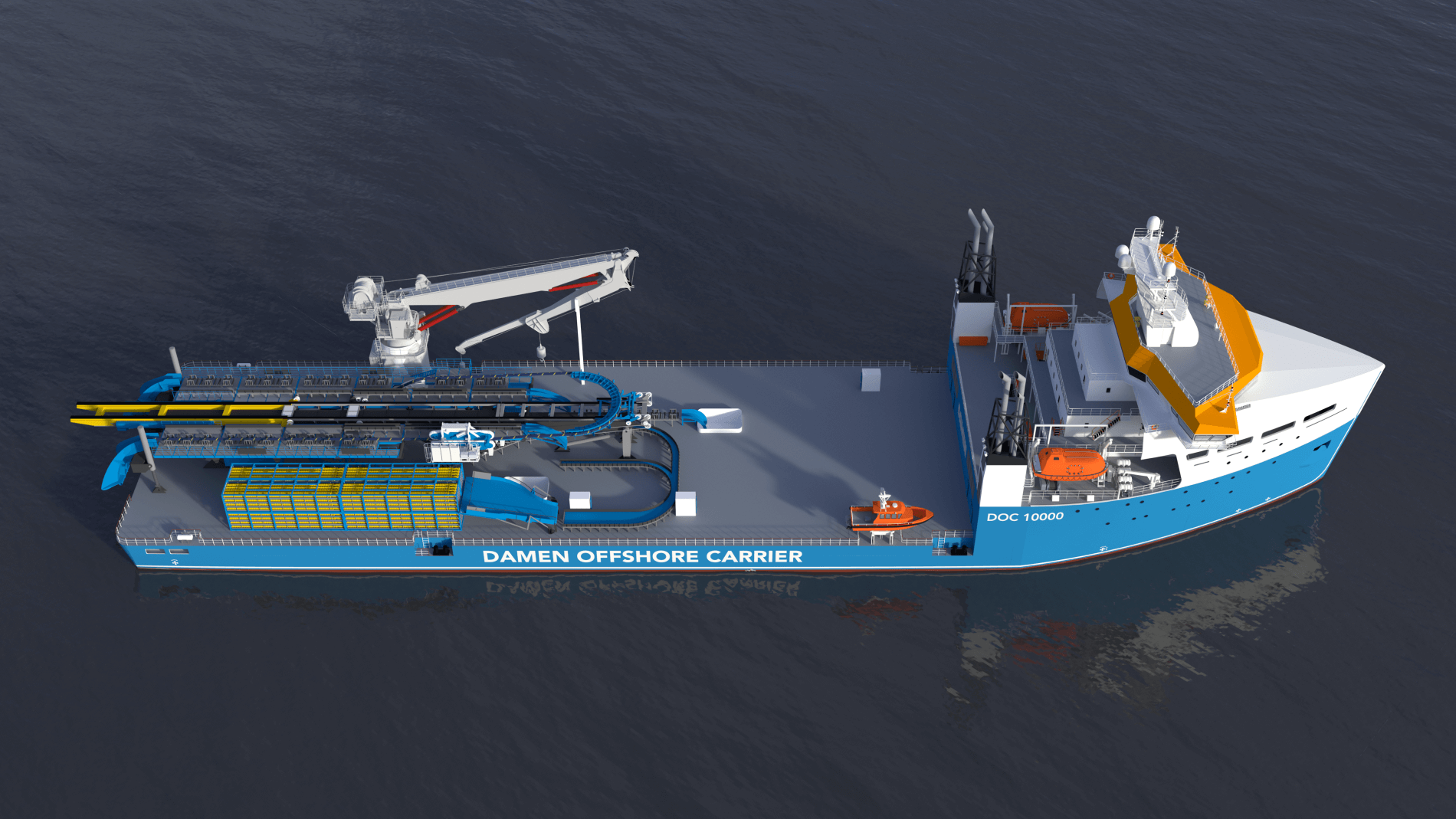
Motion compensated cable lay system provides significantly improved workability in combination with reduced risk of cable damage in several ways:
- Avoiding overbending of the cable caused by catenary dynamics
- Compression in the cable will not occur due to reduced tension variations
- Touch down point excursions are reduced therefore omitting the damage of the cable, in particular when cornering
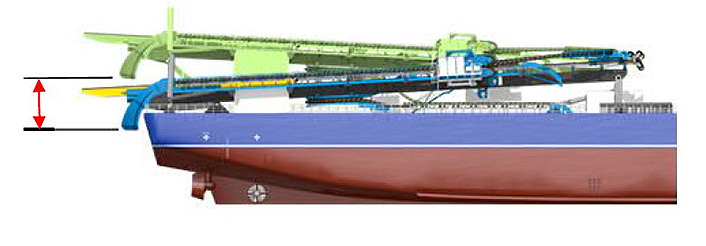
The quadrant is fully restrained from the start of the operation until deployment below the splash zone:
- Increased weather window
- Controlled and time efficient operation
- Increased safety
The quadrant handling system is equipped with a cursor system. The quadrant motions are fully restrained until deployed beneath the splash zone:
- The cursor system prevents damage to the quadrant
- Reduced catenary dynamics
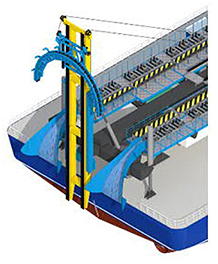
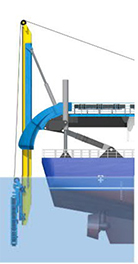
CPS strings are loaded on board in containers and transferred to the firing line using a gutter system
- Containers allow for easy transport and loading
- Height adjustable ramp to extract a CPS from different elevations
- CPS gutter system independent from cable routing allowing parallel operations
- Safe access for personnel to containers
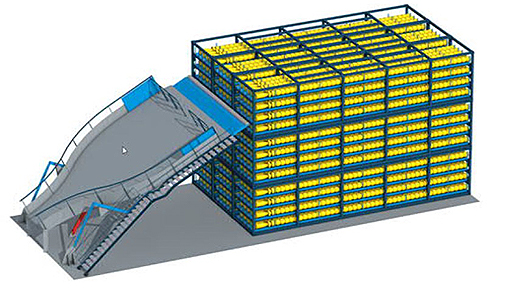
The radius of the quadrant can be adjusted from the maximum bending radius to straight during lowering
- Cable can be abandoned without uncontrolled drop onto the seabed. Cable tension is controlled during the complete operation
- Quadrant can be retrieved when cable is straight on the seabed avoiding torque variations that can cause cable failure
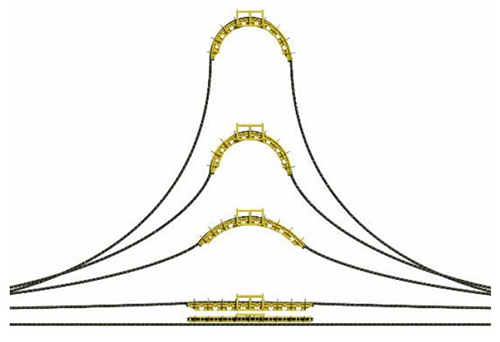
Synchronization of the Pull-in-Winch with the central control system ensures better control of pull-in operations
- Improved tension control avoids overbending or compression in the cable
- Controlled from vessel using a secure data connection
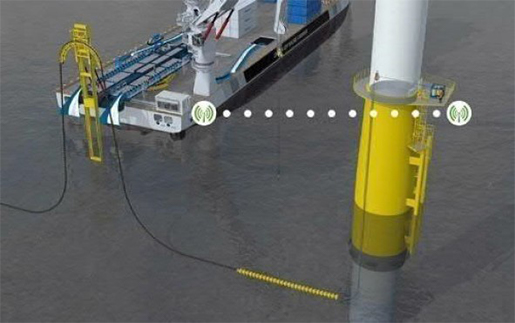
Free deck space for cargo and project equipment
- Equipment, controls, instruments and furniture are thoughtfully arranged providing optimum functionality and comfortable layout
- In collaboration with our suppliers, a selection of equipment and digitization technologies has been made with the aim of making the bridge operation easier and safer without compromising improved performance of the vessel
- An ergonomically designed bridge layout with optimal bridge visibility in accordance with the rules and regulations, 360 deg clear view on the work deck as well as the relevant deck equipment
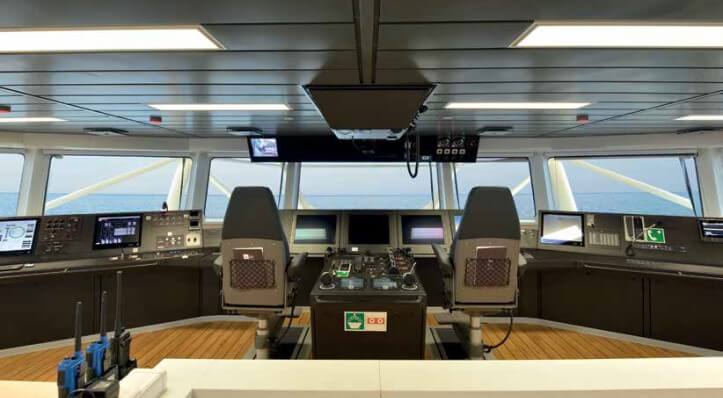
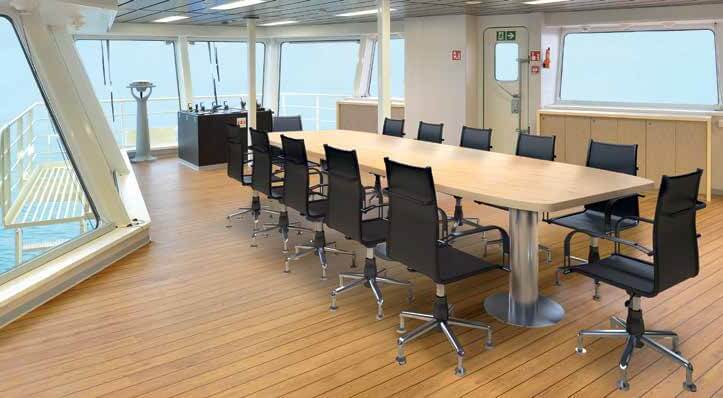
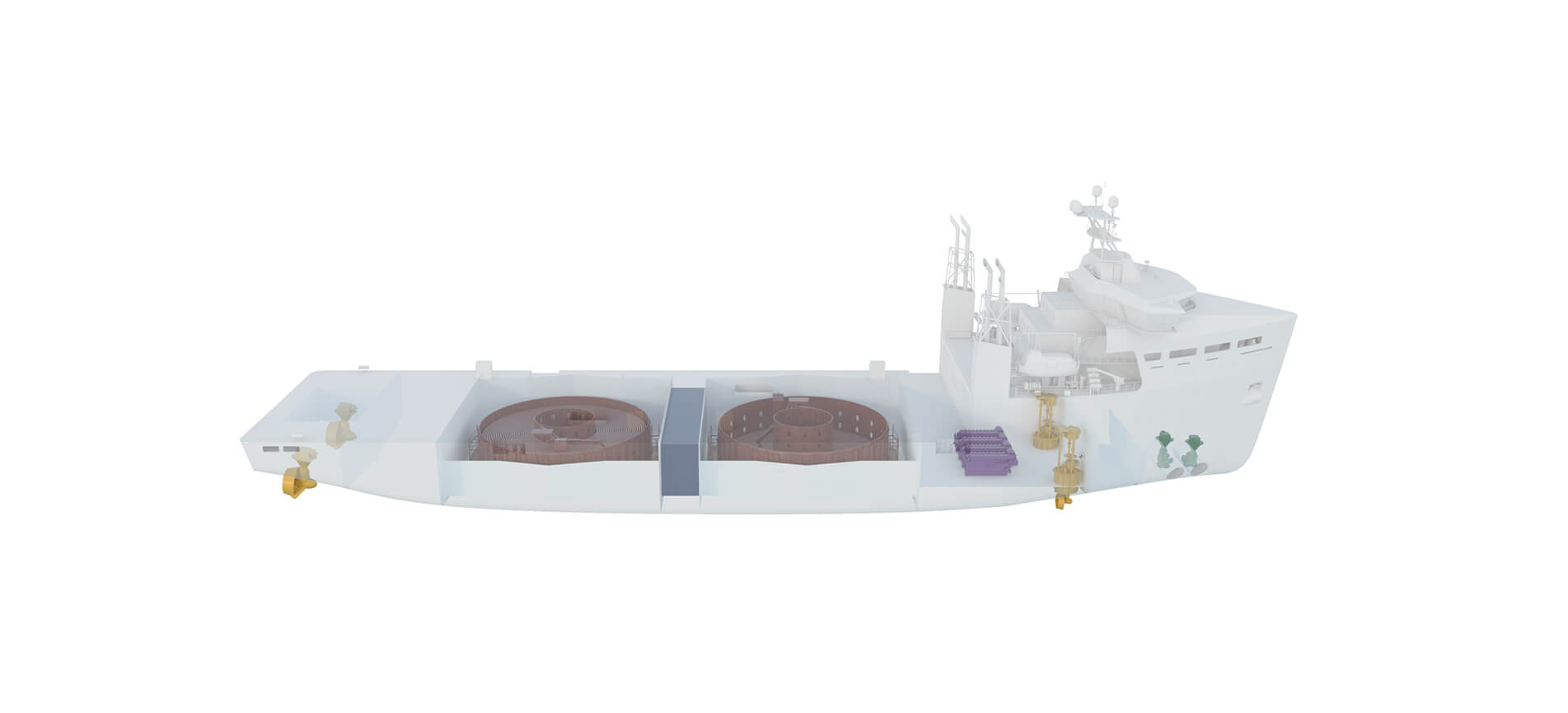
- Ample carrousel capacity (2x 4000 t) to execute any cable lay operation efficiently
- Maximum weather protection of crew and product during loading and operations
- More free deck space for storage, additional mission equipment etc.
- Free surface anti-roll tank is integrated in the vessel
- Positioning at center of the vessel results in optimal roll damping effect
- The anti-roll tank is far from the accommodation, so noise disturbance for crew is minimal
- Vessel enables station-keeping up to Hs 4.2 m (without laying cable)
- Vessel enables harsh weather cable lay operations (up to Hs 3.5m)
- Propulsion set-up:
- Azimuth thrusters 2x 3100 KW
- Retractable thrusters 2x 1400 KW
- Tunnel thrusters 2x 1400 KW
Detailed specifications
Damen Offshore Carrier 10000
Huisman Motion Compensated Cable Lay System
Delivering Value. Together.
The two companies form a natural partnership with one another. Both are well-established family businesses, with a combined track-record of over 180 years in the Dutch maritime and offshore industries. They share a drive to incorporate family values in their work. Both Damen and Huisman seek to develop long-term relationships with their clients and other stakeholders. They have a listening ear, attuned to the market and work – together as a team – to develop high quality, innovative solutions that enable a safer, more efficient and productive working environment.

Damen Shipyards Group has been in operation for over ninety years and offers maritime solutions worldwide, through design, shipbuilding, ship repair and related services. Damen operates 36 shipyards in 18 countries and offers direct employment to more than 13,000 people. Damen is also active in the repair and conversion of existing ships and the sale and production of components for the maritime industry.

Huisman, a family owned company, designs and manufactures heavy construction equipment for the world’s leading companies in the renewable energy, oil and gas, civil, naval and entertainment markets. Our products range from Cranes, Pipelay Equipment, Drilling Equipment and Winches and Specials.